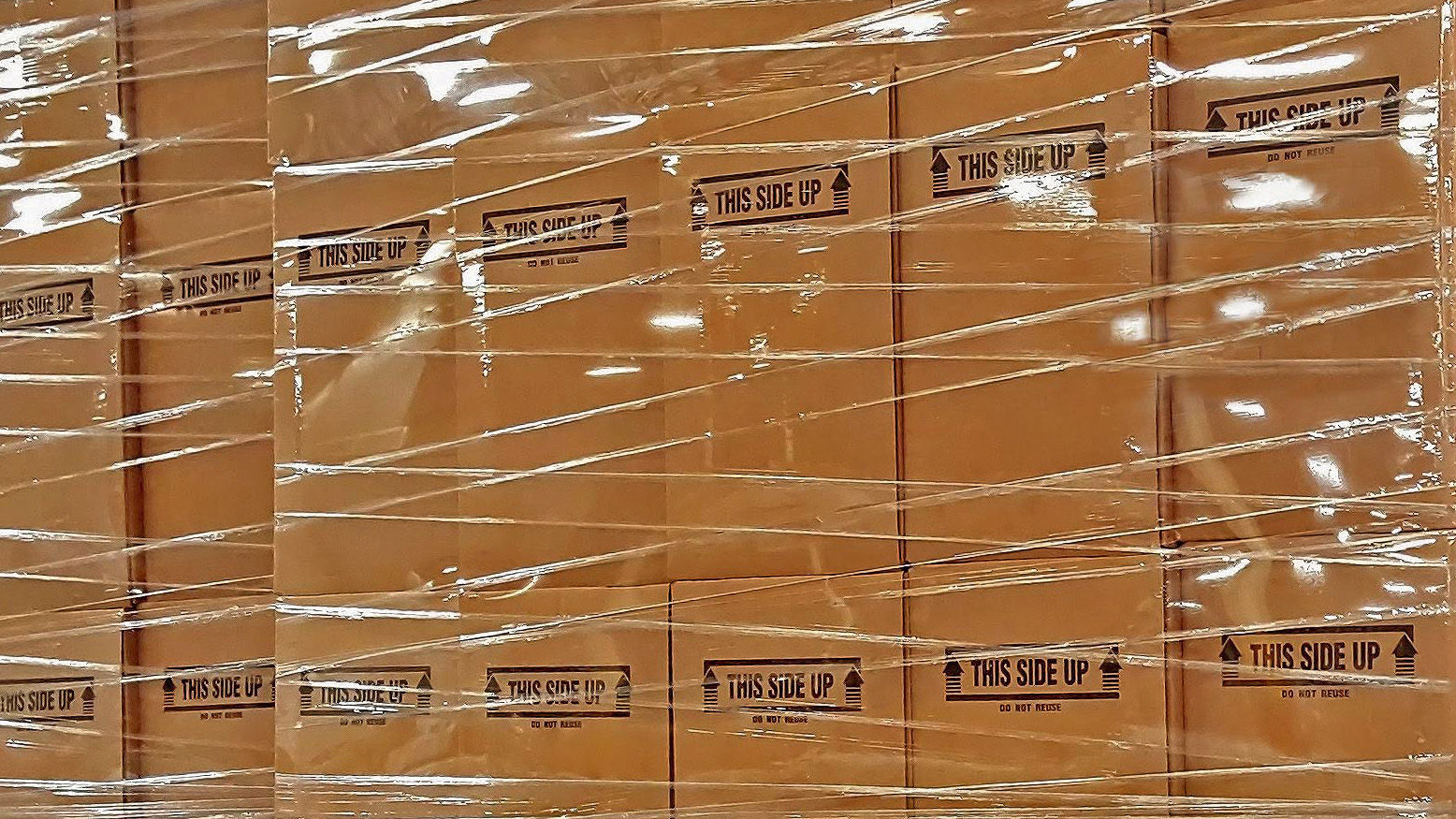
The Performance Audit Process
Upon installation of the system, our Service Engineer will establish the ideal settings on your equipment to achieve maximal savings and maximal results.
​
Your Service Engineers will record your optimized settings in our database. Then, on regular follow-up visits, they will perform a complete audit to ensure that the settings for each machine have not been changed, the load containment standard is maintained, and that you are continuing to realize the maximum cost savings and comprehensive benefits from Rapid Bander or Rapid Roper.
​
If settings have been changed, your Service Engineer will:
-
Restore the machine to optimal settings, and validate those settings.
-
Notify the department manager or key contact, so they are aware of any changes made to the system, by reporting what the settings should be and what they were changed to.
-
Provide additional training to operators so settings remain optimized.
With our regular system monitoring, you can be sure you’re getting the full savings and benefits from using a Rapid system.

Our Service Engineers will test, assess, adjust, repair and maintain our equipment - at no cost to you.
Service & Maintenance
Rapid Technologies Field Service Engineers have extensive background, experience and knowledge of equipment and programmable logic controllers (PLCs). We maintain an unparalleled training program, as well as a shared knowledge base forum for our engineers, keeping them up-to-date in the latest advances in equipment and know-how.
​
Your Service Engineer is thoroughly trained to install and service the Rapid Bander device, as well as all packaging equipment including stretch wrap machines, conveyors and tape heads.
​
Free Service and Repairs
Rapid Bander and Rapid Roper devices require almost no maintenance. When they do, we provide it at no cost to you. Our Technicians perform routine service and repairs based on our proven service checklist, so nothing is missed in keeping your equipment running at peak performance.
​
Service and repairs on your existing stretch wrappers, including a comprehensive scheduled maintenance program, can be performed at reasonable prices and plans to suit your needs.
​
Free System Performance Audits
It is one thing to set up a wrap pattern with specific settings to achieve a targeted load containment standard and a film/labor cost standard. It’s an entirely different thing to maintain it. Deviations can lead to increased load failures and excessive cost overruns.
When a system gets set up to run a new conventional stretch film, the nightmare of web breaks is often only a few wrapped pallets away. To combat the problem, the machine operators will lower the applied tension setting to try to prevent tears and punctures from propagating which causes the web breaks. But this compromises load containment. So to compensate, they will also increase the number of times the pallet is wrapped. Both changes increase the amount of film – and the cost per load - that is applied to the pallet.
When you combine this outcome with normal machine wear and tear from worn pre-stretch rollers or gears slippage, the problem becomes exponentially worse. The end result of all this is compromised load containment and considerably higher film costs, wrap time and wear and tear on equipment.
The best way to ensure that you are satisfied with our products is to make sure they perform properly. We will conduct and record detailed audits of your wrapping process and provide basic preventative maintenance at no cost, ensuring consistency and reliability, and avoiding the significant load stability issues and escalating costs that can occur.